Maximize Energy Efficiency.
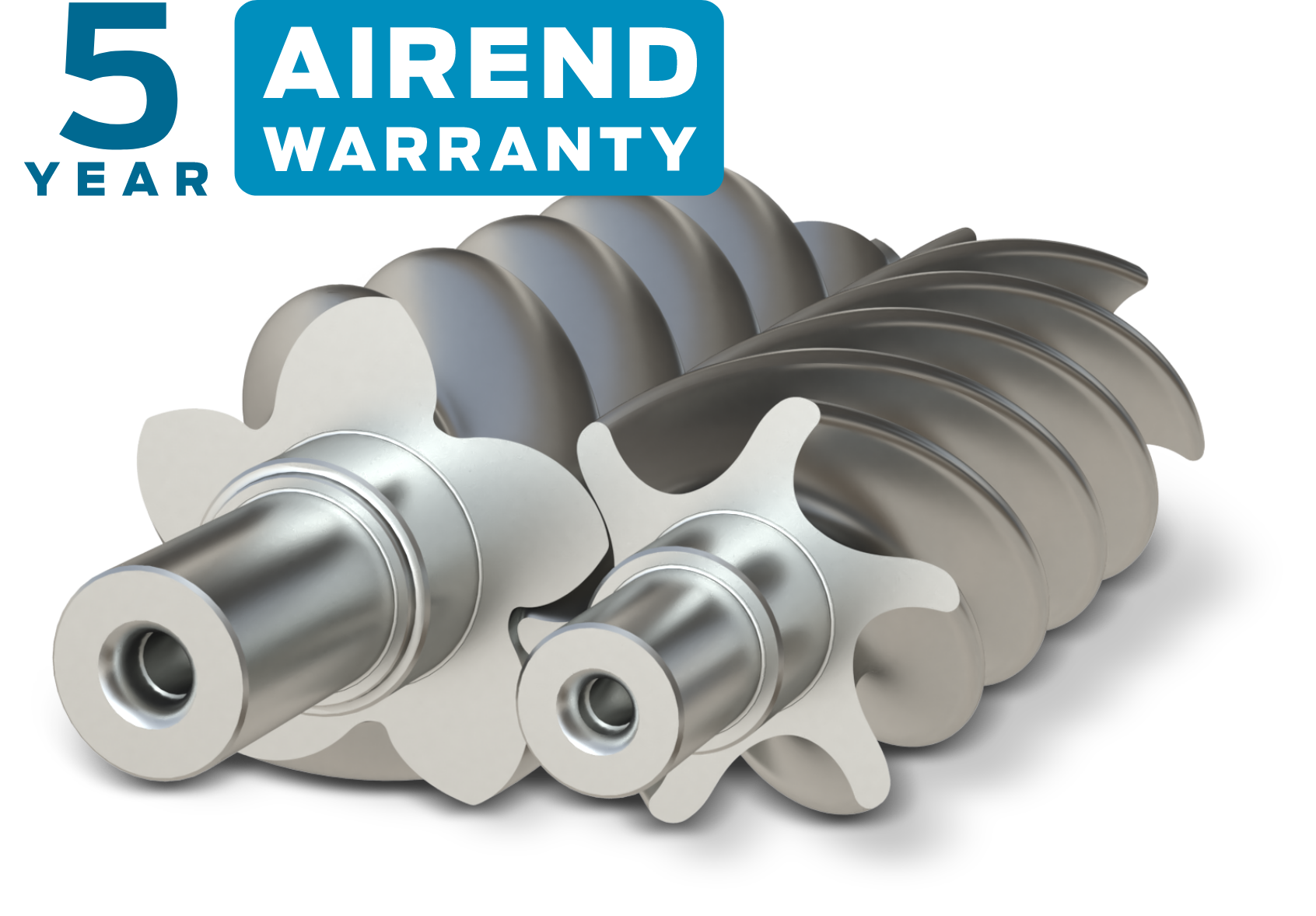
Positive Displacement Vacuum Pump Technology
Upgrade to positive displacement pumps for consistent, reliable performance in any environment. Our advanced vacuum pumps deliver stable, efficient operation with low noise, even in the toughest industrial conditions. Say goodbye to downtime and inefficiency—boost your productivity with a solution you can trust.